Human capital
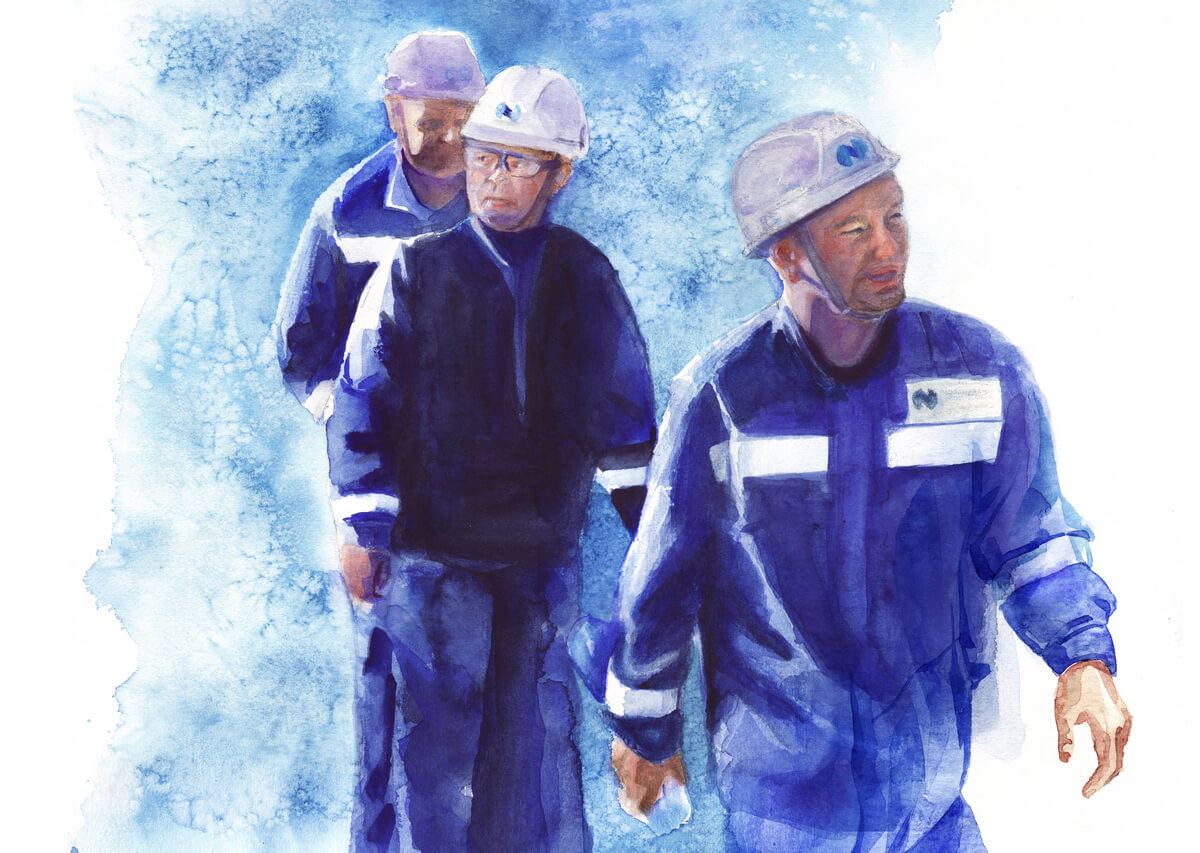
Key figures
The Group companies are parties to 23 collective bargaining agreements covering 93.7% of the Group’s
headcount.
In 2020, the Company’s health and safety indicators were some of the best in the metals
and mining industry, with LTIFR going down to 0.21 against 0.32 in 2019.
Key events and facts
During the pandemic, the Company imposed a blanket ban on job cuts and fully provided its employees
with the necessary social guarantees and support.
In 2020, the Company used the facilities of
Nornickel Corporate Health Centre LLC to launch the corporate healthcare service project.
UN Global Compact Principles
Principle 3: Businesses should uphold the freedom of association and the effective recognition of the right to collective bargaining;
Principle 4: the elimination of all forms of forced and compulsory labour;
Principle 5: the effective abolition of child labour;
Principle 6: the elimination of discrimination in respect of employment and occupation.
Health and well-being of our employees is the Company’s core value, their comfort and safety – our absolute priority. We are monitoring current developments and collaborating with federal and regional authorities to maximise the measures we are taking.
Nornickel’s efforts to combat COVID-19.
Maintaining employee safety and business continuity
The main challenge the world was up against in 2020 was the global COVID-19 pandemic.
Quite suddenly, public and private companies had to contend with the difficult task of ensuring uninterrupted and safe operations amid restrictions, national and global lockdowns, and the resultant economic downturn.
Nornickel’s key objectives during the pandemic included:
- protecting the health and safety of its employees (main priority);
- efficiently adapting business processes to new circumstances;
- supporting authorities and communities in the regions of operation.
To meet these objectives, Nornickel established an emergency response team (ERT) led by First Vice President and Head of Corporate Security Sergey Barbashev and comprised of the Company’s senior management. The team was charged, among other things, with ensuring continuity of the Company’s production, procurement and sales processes while taking all necessary measures to protect the Company’s people. Local quick response task forces were also established across our sites. The ERT held regular meetings to discuss incoming epidemiological data and develop an appropriate response. To ensure greater effectiveness of its response action, Nornickel actively interacted with federal and regional government authorities.
Timely and prompt measures cushioned the blow of the pandemic on the Company’s operations. Sales went largely undisrupted save for an occasional minor delay in or cancellation of certain shipments; there were no disruptions in logistics as almost 90% of materials and consumables come from local sources; problems with supplies of essential imported components for equipment repair and maintenance were avoided.
Thanks to its extensive vertical integration and own energy and transport capacity, Nornickel did not have much trouble maintaining business continuity and receiving/dispatching goods, meeting its production targets for 2020.
The Company is continuously monitoring the coronavirus situation in Russia and worldwide and is taking every effort to minimise risks and reduce the spread of the infection.
To support and protect its employees, the Company took the following key steps:
Occupational safety | Employee support |
---|---|
|
|
HR management
Our human capital is the basis of our success. With this in mind, Nornickel seeks to create an attractive employee value proposition to help its people fully develop their potential and boost the shared sense of engagement towards achieving the Company’s goals.
To assess the quality of HR management and ensure its efficiency, the Company continuously monitors HR metrics and reviews staff costs, productivity levels, impacts of its social and adaptation programmes, and employee engagement survey results.
- Building a skilled and balanced team
- Staff training and development
- Improving productivity
- Creating a talent pool
- Enhancing our incentive system
- Implementing our social policy
HR management responsibilities are allocated among Nornickel’s various governance bodies and business units in line with their terms of reference.
Governance body | Responsibilities |
---|---|
Board of Directors 102-26 |
|
Corporate Governance, Nomination and Remuneration Committee of the Board of Directors |
|
Senior Vice President for HR, Social Policy and Public Relations |
|
HR Department |
|
Social Policy Department |
|
HR functions of the Group companies |
|
|
Key HR management regulations* :
- Principles and provisions of the international law, standards of the International Labour Organisation, national laws of the countries of operation
- Constitution and the Labour Code of the Russian Federation
- Equal Opportunities Programme
- Freedom of Association Policy
- Working Conditions Policy
- Personal Data Policy
- Talent Pool Regulation
- Procedure for Assessing Employee Performance
Staff composition
In 2020, the Group’s average headcount was 72,319 employees, of which 99% were employed at its Russian companies.
A 2% y-o-y decrease in the average headcount across the Russian operations was due to the continued implementation of the programme to improve productivity and reduce costs.
The headcount* of the Group’s Russian companies as at the year-end stood at 73,810 employees, with most of them working full time (>99%) and on permanent contracts (>96%). As at the end of 2020, there were 910 employees working on civil contracts. 102-7 102-8
Personnel structure by gender and category in 2018–2020.*
Category | Managers | White-collar employees | Blue collar employees | |||
---|---|---|---|---|---|---|
Year/gender | Male | Female | Male | Female | Male | Female |
2018 | 8,017 | 2,639 | 6,047 | 6,911 | 40,502 | 10,810 |
2019 | 7,979 | 2,518 | 6,189 | 6,940 | 38,842 | 10,314 |
2020 | 8,117 | 2,575 | 6,436 | 7,043 | 37,352 | 9,925 |
Personnel structure by gender and age, %
Age | Up to 30 | 30–50 years | Over 50 | |||
---|---|---|---|---|---|---|
Gender | Male | Female | Male | Female | Male | Female |
% of headcount | 11.6 | 3.8 | 45.9 | 19.8 | 13.1 | 5.9 |
Key personnel turnover indicators*
Indicator | 2015 | 2016 | 2017 | 2018 | 2019 | 2020 |
---|---|---|---|---|---|---|
Employments | 15,607 | 15,166 | 11,262 | 14,901 | 13,805 | 10,481 |
Employee inflow ratio* , % | 19.1 | 18.8 | 14.6 | 19.9 | 18.8 | 14.2 |
Separations | 14,277 | 15,413 | 15,232 | 16,918 | 13,832 | 10,247 |
Employee turnover* , % | 10.7 | 10.5 | 10.3 | 10.2 | 10.5 | 9.7 |
Voluntary turnover* , % | 8.0 | 6.8 | 7.7 | 7.5 | 8.2 | 7.8 |
Employee outflow ratio* , % | 17.1 | 19.2 | 20.0 | 22.6 | 18.8 | 13.9 |
The Company is a major employer in the Norilsk Industrial District and the Kola Peninsula and as such has a significant impact on these regions’ labour markets. In hiring personnel, we assess all candidates based on their work experience, qualifications, and education.
In 2020, the Company employed 546 new permanent staff members from other regions of Russia.
The share of top executives from among local communities was 99.7% across the Group’s Russian companies in 2020. 202-2
The share of employees from among local communities* was 99.7% across the Group’s companies in 2020.
Strong employer brand
In 2020, we retained leadership in key Russian and international rankings of the best employers:
- best employer in the metals and mining industry among students, graduates and international rating experts according to Universum and Randstad Award;
- best employer in the metals and mining industry among students of leading universities, according to Best Company Award;
- a top 3 employers in the metals and mining industry according to Future Today’s opinion survey of Russian universities;
- a top 20 position among 100 best employers in Russia according to HeadHunter’s 2019 ranking.
Commitment to employee rights
Respect for employees and their rights lies at the heart of Nornickel’s business.
The Company employees’ working hours are set by internal labour regulations approved by the Company with due regard to the opinion of the trade union. The Company has a standard working week of 40 hours as determined by the applicable Russian laws and regulations. Employees involved in harsh, hazardous and/or dangerous work enjoy a reduced working week of not more than 36 hours. Women employed in the Far North and equivalent areas are accorded 36 hours of work per week unless reduced by Russian laws and regulations. The Company arranges for accurate time and attendance control for each employee.
Nornickel does not tolerate child labour in any form, including the involvement of minors below 18 in hazardous and/or dangerous work. The Company strictly complies with the applicable regulations prohibiting women’s exposure to harsh and dangerous work in the mining industry.
Employment of people with disabilities
As part of our efforts to employ people with disabilities in line with Russian statutory requirements, we provide them with necessary working conditions, including work and rest schedule, annual and additional paid leaves, and specialised workspace equipment.
According the employment quotas that vary depending on the region and company size, the share of such employees starts from 2% of the average headcount, excluding employees involved in harsh, hazardous and/or dangerous work.
At the same time, we provide our employees with equal opportunities to develop their professional potential. Employee performance is evaluated on a fair and impartial basis, and recruitment and promotion decisions are tied exclusively to professional abilities, knowledge, and skills.
The Company implements programmes for the development and social support of its employees, upholding their rights in respect of social security, education, family welfare, shelter, freedom of artistic expression, and participation in cultural life.
Offices for operating, social and labour relations
In addition to the Corporate Trust Line, the Company has offices for operating, social and labour relations in place. They are primarily tasked with response to employee queries, control of their processing, prompt resolution of conflicts and preventing violations of employee rights.
The offices regularly monitor the climate within the teams, enabling the Company to address any arising issues in a timely manner.
In 2020, the Group companies operating in the Norilsk Industrial District ran 24 offices that received over 40,000 queries from employees (81%), former employees (18%) and local communities (1%). They focused on social and working matters (79%), legal matters (20%) and other topics (1%).
Social partnership framework
Nornickel Group companies have a social partnership framework in place, which operates to reconcile the interests of employees and their employing organisations on matters pertaining to social and labour relations. The Company performs its obligations in compliance with the Labour Code of the Russian Federation, collective bargaining agreements, the interregional cross-industry agreement for copper and nickel producers and their supporting industries for 2019—2022, and joint resolutions. We also follow the Freedom of Association Policy approved by the Board of Directors. 102-41
In labour relations, employee interests are represented by social and labour councils and trade unions.
All the Group’s major companies operating in the Norilsk Industrial District and Murmansk Region have in place social and labour councils representing workers. Chairs of the local councils make up the Social and Labour Council of MMC Norilsk Nickel and the Social and Labour Council of Kola MMC.
The Group companies have collective decision-making bodies representing the employer, employees and trade unions, including collective bargaining commissions, labour dispute commissions, social benefits commissions, social insurance commissions, health and safety commissions, social and labour relations commissions, etc.
The Trade Union of MMC Norilsk Nickel Employees, an interregional public organisation that includes territorial trade unions and trade unions of the Group companies, represents the Group’s employee interests on the interregional level. The trade unions of transport and logistics divisions are members of the Yenisey Basin Trade Union of Water Transport Workers (Krasnoyarsk, Russia).
The Group companies are parties to 23 collective bargaining agreements covering 93.7% of the Group’s headcount. As at the end of 2020, 8.4% of all the Group’s employees were members of trade unions, while 78% were represented by social and labour councils. 102-41
The Company complies with the Labour Code of the Russian Federation setting out the minimum notice period in case of significant organisational changes (at least two months prior to the start of such changes or three months prior to the start of such changes in case the redundancy decision may lead to large-scale dismissals). These standards are formalised in collective bargaining agreements. 402-1
The absence of strikes and lockouts involving the Company’s personnel in the reporting year testifies to the effectiveness of Nornickel’s employee interactions and its social policy at large. MM4
In order to develop interregional social partnerships, Interregional Cross-Industry Association of Employers “Union of Copper and Nickel Producers and Their Supporting Industries” and the Trade Union of MMC Norilsk Nickel Employees signed an interregional cross-industry agreement for copper and nickel producers and their supporting industries for 2019– 2022. The agreement regulates social and labour relations between the employers who are members of the association and their employees and sets out common approaches to employee remuneration, compensation and benefits, work and rest schedule, health and safety, dismissals and other matters. In 2020, to align the agreement with new laws, the parties signed amendments thereto.
As at the end of 2020, the agreement applied to 22 Group companies, including MMC Norilsk Nickel, covering 88.5% of the Group employees.
In December 2020, the Company and the Trade Union of Company Employees as well as Kola MMC and the trade unions of Kola MMC signed agreements defining goals, key focus areas and obligations of the parties to foster social partnerships.
Remuneration policy goals | Remuneration policy principles |
---|---|
|
|
Incentives and rewards
Nornickel has a robust employee incentive programme with both financial and non-financial rewards designed to retain top talent and motivate our employees to enhance their performance and help drive the Company’s business growth.
The use of financial rewards is governed by the Company’s remuneration policy.
Nornickel’s grading system is designed to maximise its return on investment in human capital and to attract, engage and retain top talent. Grading relies on the point factor method of job evaluation that takes into account knowledge and skills, the complexity of tasks, and the level of responsibility.
In 2020, we introduced a new project-based incentive framework for all staff of capital construction PMOs, which replaces a traditional annual bonus with the reward for the success of the project or its stage. Linked to key project indicators, bonuses seek to motivate and retain key talent until the project is completed.
Corporate culture development
As part of its human resource strategy, Nornickel seeks to develop its corporate culture with a focus on improving efficiency, accountability and employee engagement.
Updated Business Ethics Code
On 18 December 2020, the Board of Directors approved the new version of MMC Norilsk Nickel’s Business Ethics Code.* .
The Code sets out the core corporate values guiding the Company’s activities, highlights the absolute priority of occupational health and safety, describes the responsibility to employees, investors, the society and environment, and defines requirements to be observed by employees with respect to the Company’s resources, information disclosures, conflict of interest and workplace interactions.
To this end, we have set up change management teams across the Group companies to develop and implement action plans to improve their staff engagement. MMC Norilsk Nickel provides expert support to the teams, which includes regular training sessions, feedback, audits, and guidelines.
For the third year running, the Company has been implementing a project focused on building a culture of dialogue between management and staff at all levels. The project seeks to increase awareness, ensure that employees are committed to the Company’s goals and values, and improve trust between workers and leadership. In 2020, it featured 32 corporate dialogues, 90 sessions with the management of Group companies, the online conference “Challenges-2020: Pandemic, Environment and Safety” attended by more than 10,500 people, an information campaign on how the metals and mining industry copes with the crisis covering over 14,000 people, and a unique three-hour live stream Nornickel Live with the vice presidents answering employee questions. In total, 5,500 people took part in these events in 2020
Employee engagement and corporate culture workshops were included in the 2020 agenda of ten conferences in various functional areas as well as the curriculum of the Company’s training programmes (Nornickel’s Leaders and Pursuing Efficiency) and enrolled over 1,000 employees.
In addition, every year, we implement a set of measures to drive employee engagement. They include a corporate employee engagement survey named “Let Everyone Be Heard” run by an international HR consultancy firm based on questionnaires and focus groups, which is followed by the review of the survey results, and implementation of improvement initiatives.
The 2020 survey covered more than 30 Norilsk Nickel companies and was completed by 42,600 employees of the total headcount. Its completion rate exceeded 61%, which means that the results of the survey are representative of the Group as a whole.
Based on the survey results, employee engagement across the Group grew by 4 p. p., with the highest growth of 4 p. p y-o-y achieved in the following categories: top management, respect and acceptance, performance management, remuneration and recognition, and success factors.
Employee awards
To foster engagement and recognise employee achievements, the Company offers non-financial incentives and rewards of various categories and levels. These include government awards, ministry and agency awards, regional and municipal awards, as well as the awards granted by MMC Norilsk Nickel and the Norilsk Nickel Group companies.
Key compensation indicators in 2020, by region
Region | Remuneration package, RUB ‘thousand | Average monthly salary, RUB ‘thousand | Share of regional payroll in total payroll, % | Minimum monthly compensation to statutory minimum monthly wage* | Statutory minimum wage |
---|---|---|---|---|---|
Group average | 141.0 | 131.8 | 100.0 | ||
Norilsk Industrial District (NID) | 138.2 | 129.1 | 64.7 | 1.0 | 31,538 |
Kola Peninsula Industrial District (Murmansk Region) | 103.8 | 96.6 | 12.5 | 1.0 | 27,899 |
Krasnoyarsk Territory (excluding NID) | 86.9 | 84.6 | 3.8 | 1.0 | 12,130 |
Trans-Baikal Territory | 138.5 | 132.4 | 4.0 | 1.0 | 18,195 |
Moscow and other regions* | 307.5 | 285.4 | 15.1 | 2.48 | 20,195 |
The Company rewards employees for their outstanding performance, innovations that drive growth, add economic value or deliver meaningful efficiency gains for the Group or a Group company, and efforts that go beyond formal agreements and contribute to the Company’s success.
The Company has a range of corporate awards designed to celebrate employee achievements.
In addition to a corporate award, the employee receives a one-off bonus. MMC Norilsk Nickel’s badge of honour, the highest corporate award, entitles its owner to a one-off payment, as well as a lifetime corporate pension.
The best employees may be nominated for agency (industry) and government awards. The Company welcomes the recognition of its employees’ accomplishments by the government and its agencies and proudly nominates them for various awards to highlight their prodigious operational and management achievements, and significant contribution to production growth.
In 2020, 22 Nornickel employees received medals of the Order “For Merit to the Fatherland”, 2nd Class, for specific achievements beneficial for the industry and the nation at large. Four employees received Honoured Metallurgist of the Russian Federation titles, while another ten were named Honoured Miners of the Russian Federation.
The reporting year saw a total of 3,900 Company employees receive various awards, including: 54 and 254 honoured with government and ministry/agency awards, respectively, 1,249 who received awards from regional and municipal authorities, 580 and 1,767 who were granted corporate and local awards of the Group companies.
Personnel training and development
We need to make sure that we have highly skilled and competent workforce to support the Company’ production upgrades, onboard new technology and leverage innovations. This is why continuous training plays a key role in Nornickel’s personnel development
Our training programmes cover all functional areas and all employee categories. 404-2
The Group’s employees can benefit from free staff training, retraining, skills improvement, and internship programmes funded by the Group companies. The Company engages external education providers (universities, professional development institutions, research institutes, training centres, and consultants), while also training employees at its own corporate training centres. In 2020, 17,000 employees took courses in such centres.
We are going through an active transformation, which means toughening our production standards, improving employee communications and creating unique social projects. Technology and digitalisation are at the heart of our success in these areas.
Amid the COVID-19 pandemic, most of our training programmes migrated online thanks to the launch of the Nornickel Academy education platform. The platform offers more than 60 courses, some of which include recommendations and guidelines on remote work.
Nornickel’s Leaders 2.0 programme
In May 2020, Nornickel’s Leaders 2.0 training programme for managers came to an end. The training was completed by 52 managers of Nornickel facilities. The programme comprised several modules to develop managerial competencies and projects to improve business processes in the Company. The trainees were divided into five cross-functional teams and worked on the projects to boost efficiency of their units.
The pandemic made it impossible for them to complete the programme offline, and the Company decided to transition it online.
The programme expert panel made up of the Company’s vice presidents noted tangible progress in the competencies and motivation of the trainees. Their projects demonstrated the possibility of using lean manufacturing tools to make business processes more efficient, and a high level of the owners’ engagement in the projects.
Key personnel training indicators
Indicator | 2016 | 2017 | 2018 | 2019 | 2020 |
---|---|---|---|---|---|
Total training man-sessions, including training, retraining and skill improvement, thousand | 70.0 | 95.0 | 87.5 | 90.8 | 70.9 |
incl. blue-collar employees | 37 | 54 | 43.3 | 40.5 | 30.6 |
incl. managers | 22 | 26 | 27.4 | 30.9 | 23.2 |
incl. white-collar employees | 11 | 15 | 16.8 | 19.4 | 17.1 |
Employees trained, thousand | — | 46.3 | 44.0 | 40.4 | 36.7 |
Total training man-hours, thousand | 5,666 | 6,630 | 4,508.7 | 4,655.9 | 3,462.2 |
Average annual training hours per employee trained | 80.8 | 70 | 51.6 | 51.3 | 48.8 |
Average annual training hours per employee (based on average headcount) | 69.8 | 85 | 60.2 | 64.0 | 48.5 |
incl. blue-collar employees | 77.9 | 95 | 62.2 | 69.2 | 48.3 |
incl. managers | 72.4 | 83 | 76.7 | 72.5 | 64.0 |
incl. white-collar employees | 31.9 | 44 | 38.7 | 37.5 | 36.8 |
Training costs, RUB mln | 760 | 896 | 1,022.2 | 1,101.9 | 740.2 |
Costs per employee trained, RUB | 10,841 | 9,459 | 11,687 | 12,133 | 10,440 |
Pursuing Efficiency programme
The key focus was made on the projects selected by the participants at their discretion. The crossfunctional non-expert teams were very productive, coming up with actionable quick wins. Many of them gained a better insight into the actual business process, strengthening interactions between employees from various functions. As part of the offline stage, the participants could visit another facility and do some real field work.
The key focus was made on the projects selected by the participants at their discretion. The crossfunctional non-expert teams were very productive, coming up with actionable quick wins. Many of them gained a better insight into the actual business process, strengthening interactions between employees from various functions. As part of the offline stage, the participants could visit another facility and do some real field work.
Our large-scale programmes for managers help lay a strong foundation for the Company’s future development and boost efficiency while also reshaping the management perception of other corporate values, namely reliability, growth, collaboration, professionalism, and responsibility, and changing their mindset as well as the stewardship style and toolkit.
In December 2020, our training courses for top and middle managers fully migrated online and were tweaked to match the new learning environment.
Online training has given us a unique experience – we launched the programme in one reality and finished it in another. Online will certainly not replace offline, but we have done very well and now have valuable expertise under our belt. I have every confidence in the graduates’ success, and the projects they presented and defended will add value to the Company.
360-Degree Management programme
In August 2020, the managers who had undergone a 360-degree competency review also completed the 360-Degree Management programme focused on enhancing corporate and managerial competencies. Each participant could select one of six topics: people management, execution management, developing corporate competencies, communications, systemic thinking, and partner relations. This marathonformatted programme is distinct in its brevity and effectiveness, with homework incorporated into day-to-day management. The 360-Degree Management programme was completed by 124 managers from 18 divisions, Group companies and the Head Office.
Project Environment development programme
In 2020, we launched a Project Environment programme to create a knowledge base and project management tools for the employees involved in corporate investment projects.
It comprises two subprogrammes:
-
PM (Project Management) for heads of capital construction PMOs. Its participants were 47 managers
of the Group companies.
The subprogramme includes six modules covering the entire investment project life cycle with a focus on engineering competencies and soft skills in HR and contractor management. The subprogramme spans 2020—2021 and features guidance from the leading Russian and international experts. Its participants study global trends, practices and advanced tools in project management, such as value engineering, planning and technical support of material and equipment supplies, construction quality control and planning, cost engineering, and risk and contract management. - Professional subprogramme for line managers and experts involved in capital construction projects. The subprogramme comprises eight modules seeking to upskill employees in different functional areas. In 2020, it was completed by 114 employees of capital construction PMOs.
We will be working to implement an ambitious capital construction programme in 2020—2030. To achieve this goal, we need qualified managers capable of initiating projects and achieving success at every stage of their life cycle in line with corporate objectives, and top-notch engineers able to find their own solutions to challenges arising in the course of capital construction
Talent pool
To ensure availability of highly qualified managerial personnel for the Group’s operations, Nornickel relies on continuous professional development planning for its employees, builds a talent pool for leadership positions, trains and promotes pool members.
In 2020, the Company continued to roll out the talent pool management programme for junior and mid-level managers at its Norilsk site, and updated the talent pool of Norilsk Division’s core facilities. Due to pandemic-related restrictions, the Corporate University trained talent pool members online, with a stronger focus on the use of managerial skills at work. We put in place short guides to navigate project milestones for new trainees. In 2020, our Norilsk site facilities continued the roll-out of Talent Pool, an automated SAP HCM-powered system to boost talent pool management efficiency and enable data consolidation into a single database.
Career guidance and recruitment of young talent
Nornickel actively connects with young graduates, students and schoolchildren as part of its leadership, internship and career guidance programmes designed to assist the Company in attracting the best talent.
We closely cooperate with higher educational institutions and have cooperation agreements in place with 25 universities across Russia.
Despite the remote work arrangement in 2020, our Head Office carried on with the internship programme. Top Moscow-based students were invited to take part in paid internships at the Company’s Moscow office. The programme enjoyed strong demand, with over 2,000 students applying for enrolment and 11 selected as participants.
Nornickel places a strong emphasis on promoting engineering education in Russia, helping to boost interest in engineering careers among young people. In 2020, we supported CUP Technical, Russian and international case competitions among students of technical universities. They challenged students to develop solutions to business cases dealing with Nornickel’s operations, giving them valuable insights into the Company’s business.
To continue with the Conquerors of the North programme during the pandemic, we decided to transition it online. An effective talent pool building tool, the new programme became our maiden course to help young engineers develop skills necessary to work in production. By dealing with cases using applied problem solving methods, they gained an insight into real engineering challenges, while soft skill training was useful for those aiming for a successful career and outstanding results. After completing the programme, 226 trainees were recommended for internship and further employment at Nornickel.
The reporting year saw the second enrolment to the First Arctic 2.0 leadership programme for graduates and young professionals, with over 3,734 people filing applications and only 25 offered employment at Group companies after the assessment. Following intensive training, participation in corporate projects and internships at various functions, the trainees will be offered managerial positions at Nornickel sites.
Also, we run a number of career guidance initiatives for schoolchildren. They include Arctic.PRO R&D Winter School, Arctic Wave festival of R&D discoveries, IMake engineering marathon, School of Urban Competencies and the School Break educational project – all attended by over 29,500 schoolchildren annually.
Occupational health and safety
Occupational health and safety is one of Nornickel’s strategic priorities. As a company engaged in mining, concentration and smelting operations, running many hazardous production facilities, and using various hazardous substances in its processes, we are aware of our responsibility for life and health of production workers, both our own and those employed by contractors.
Nornickel's Occupational Health and Safety Policy gives precedence to the life and health of employees over operational performance while also demonstrating the Company’s commitment to creating a safe and healthy environment and fostering sustainable employee motivation for safe workplace behaviour. In 2020, the revised Occupational Health and Safety Policy of MMC Norilsk Nickel was updated and approved by order of the Company’s President.
Zero work-related fatalities and an ongoing reduction in overall workplace injuries are the Company’s key strategic priorities in OHS.
Health and safety management
Occupational health and safety (OHS) at Nornickel is governed by Russian laws, international regulations and standards, and internal policies and regulations. All of Nornickel’s Russian business units have in place the occupational health and safety management system that serves to ensure the safety of both the Company’s and contractors’ employees.
OHS regulations: 403-1
- Applicable Russian laws aligned with international laws, including conventions of the International Labour Organisation
- Occupational Health and Safety Policy
- Occupational Health and Safety Strategy
- Corporate OHS standards (17 in total)
- Regulation on the Health and Safety Management System
- OHS sections in collective bargaining agreements for the Group’s Russian operations
- Regulations and guidelines for all production processes
- Project implementation plans and specifications for repair, construction and installation works
- Health and safety guidelines for specific jobs and types of work at all of the Company’s facilities
In 2020, a new Regulation on the Company’s Health and Safety Management System that fully complies with the requirements of ISO 45001:2018 was developed and approved, and the Company adopted a new corporate OHS standard – Procedure for Organising and Conducting Hot Works
Starting 2020, the Company has in place the Corporate Standard on Management Commitment to Occupational Health and Safety. Managers draw up personal OHS commitments for the year, which include personal meetings with employees at production units, participation in audits of the health and safety management system, and holding of the Engineer’s Day with line managers. Achievement of the personal targets is reflected in the management’s KPIs, and production unit managers are remunerated based on OHS indicators. These indicators make up from 5% to 36% of the KPI sheets, with fatal accidents serving as a blocking factor that reduces the OHS score to zero.
Occupational health and safety responsibilities are allocated among Nornickel’s various governing bodies and business units in line with their terms of reference.
Governing body | Responsibility |
---|---|
Board of Directors 102-26 |
|
First Vice President and — COO* |
|
HSE Committee |
|
HSE Department |
|
Contractor safety management
MMC Norilsk Nickel procures production and technical supplies on the domestic market under Master Agreements: a separate standard-form agreement is signed with each supplier as part of centralised procurement by MMC Norilsk Nickel and the Group’s Russian business units, as well as for local purchases by Polar Division. Under the master agreement, a contractor recognises and commits to generally accepted principles in human rights (which include health and safety) and labour relations, as stipulated by international regulations and in particular the UN Global Compact.
Contractor operations (repair, construction and installation works at the existing facilities) are classified as high-hazard and governed by the respective corporate standard. Work permits, operations certificates and work execution plans (process sheets, guidelines, etc.) must contain safety requirements to be met when organising and performing work. The Company checks compliance with these requirements during each shift.
Prior to commencement of work, contractors’ staff receive pre-job and ad hoc health and safety briefing, including security measures set forth in work execution plans.
Nornickel has developed and introduced a dedicated standard to improve control and safety of work performed by contractors at its facilities. The standard sets out relevant requirements applicable to contractors at the selection stage and onwards.
In 2020, we consistently implemented it and monitored compliance with its requirements. In particular, we held joint inspections of compliance with safety requirements at work, and OHS council (committee) meetings involving contractor representatives. In case of failure to comply with OHS requirements, contractors were fined. The total amount exceeded RUB 17 mln in 2020.
In 2020, following an internal pre-certification and external certification audit, the Company was certified to comply with ISO 45001:2018 Occupational Health and Safety Management Systems.
OHS system development and mitigation of key risks
As part of our strategic goal to reduce the occupational injury rate, the Company seeks to continuously improve the elements of its occupational health and safety framework.
In 2020, Nornickel continued to implement the Control, Management and Security Automated System (CMS AS) as part of the Occupational Health and Safety Process Management System Implementation Programme.
CMS AS is an information system based on the SAP EHSM software that collects, processes, registers and analyses occupational health and safety information.
During the year, CMS AS was put into commercial operation at Norilsk Production Support Complex, NTEC, Norilskpromtransport, Taimyr Fuel Company, and Polar and Murmansk Transport Divisions of MMC Norilsk Nickel.
In 2021, we plan to continue rolling out CMS AS to the rest of the Group subsidiaries.
Nornickel is also implementing the Technological Breakthrough programme to improve production efficiency, automated operational control, and industrial safety. The changes cover all Operating Unit businesses and all production stages – from mining ore to making metals.
From 2017, Nornickel has been implementing the Concept for Upgrading the Rock Bolting Systems in Underground Mines to improve the safety of mining by, among other means, minimising human presence in unsupported areas of the mine and thus mitigating the rockfall risk.
Polar Division, Polar Construction Company and Kola MMC installed protective covers on special-purpose machinery used for lifting workers in the process of underground capital construction and mine preparation works.
Occupational health and safety certification
MMC Norilsk Nickel (Head Office, Polar Division, Polar Transport Division, Murmansk Transport Division) | ISO 45001:2018 |
Kola MMC | OHSAS 18001:2007 |
Pechengastroy | ISO 45001:2018 |
Norilsknickelremont | GOST 12.0.230-2007 (interstate standard identical to ILO-OSH 2001)* . |
Norilsk Nickel Harjavalta | ISO 45001:2018 |
Provision of personal protective equipment
As the Group’s employees are exposed to hazardous and harmful workplace factors (underground work, operation and maintenance of mining equipment and heavy self-propelled vehicles, extreme climate, etc.), it provides them with personal protective equipment (PPE) in addition to implementing technical and organisational safety measures. 403-3
To supply comfortable best-in-class PPE in line with the corporate standard, the Company’s production sites run preliminary tests on PPE, including the most advanced equipment from leading manufacturers
To effectively monitor safe working behaviour, the Company makes employees with a track record of up to three years wear red helmets with the word “Warning” and protective clothing with “Warning” badges.
In 2020, the Group companies spent on PPE procurement some RUB 3 bn or RUB 49,000 per employee.
Employees working in contaminated conditions are supplied with wash-off and decontaminating agents free of charge.
Nornickel has developed and implemented a standard for the identification and management of occupational health and safety risks. Certain risk management frameworks were audited as part of second party audits. The Company worked consistently to comply with the standard requirements and further improve its hazard identification procedures, assess and manage occupational health and safety risks, including verification of risk registers, drawing up and revising risk lists, making and implementing risk mitigation action plans. The standard provides for a procedure where employees can refuse to work if they believe that the workplace conditions may cause injuries or damage to health. This procedure is formalised in collective bargaining agreements. 403-2 403-3
Special assessment of working conditions
In 2020, the Company carried out a special assessment of working conditions at Polar Division, Polar and Murmansk Transport Divisions, Medvezhy Ruchey, Pechengastroy, GRK Bystrinskoye, Norilsk-Taimyr Energy Company, Norilskgazprom, and at other production facilities, in accordance with the Federal Law On Special Assessment of Working Conditions. It covered more than 14,000 workplaces and over 23,000 employees, which amounted to RUB 15 mln in expenses for the Group’s operations.
Prevention of occupational diseases
To prevent occupational diseases, Nornickel exercises regular health monitoring of personnel. Employees undergo compulsory pre-employment, regular and ad hoc medical examinations and check-ups organised at the Company’s expense. Those that have contact with hazardous materials are subject to additional examinations held at least once in five years by occupational pathology centres or other organisations authorised to conduct pre-employment and regular check-ups. These serve to assess occupational health fitness and determine if the disease is job-related. 403-3
In 2020, the Group’s costs related to medical examinations and maintenance of medical aid posts amounted to RUB 370 mln and RUB 760 mln, respectively.
The Company’s facilities have their own medical aid posts to perform pre-shift and pre-trip check-ups and provide medical assistance to employees upon request.
To automate the pre- and post-shift check-up process, the Company implements an electronic health check-up system. It was put into operation at Polar Division, Kola MMC, GRK Bystrinskoye, and Norilskgazprom.
The Company put in place contactless breath alcohol screening devices to prevent intoxicated employees from accessing production facilities. The devices are running at Polar Division (mines, Copper Plant), Medvezhy Ruchey, GRK Bystrinskoe and Norilsk Production Support Complex.
The Company provides employees working in harmful and hazardous conditions with free foods, milk, and other equivalent food products for therapeutic purposes in compliance with the applicable Russian legislation and corporate policies. In 2020, food and milk costs across the Group amounted to RUB 1.2 bn.
In case of hazardous production factors identified as part of a special assessment of working conditions, the Company provides affected employees with free personal protective equipment, including respiratory protection (respirators, gas masks), hearing protection (earmuffs, earplugs), eye protection (glasses/goggles with UV filters, visors), skin protection (gloves, protective and regenerative creams, protective outwear).
Corporate healthcare
Employee health is key to sustainable and efficient development of the Company. In 2020, the Company used the facilities of Nornickel Corporate Health Centre LLC to launch the corporate healthcare service project. 403-3 403-6
Workshop Healthcare Service* , 1 is to be established as the primary care setting to improve the availability of diagnostic and preventive services to employees. If doctors are constantly present at production facilities, they can not only render emergency aid but also provide preventive care and monitor employee health. The workshop physician will be responsible for offering professional medical services, preventing lost-time illnesses, professional diseases or disabilities, improving sanitary and hygienic conditions for employees, rendering first aid in the event of acute intoxication or disease.
In 2021, Nornickel Corporate Health Centre will employ several hundred medical professionals arriving from other regions of Russia under long-term contracts. The Company is going to provide them with housing at its own expense.
The central outpatient facility covering an area of more than 700 m2 in Norilsk will be Corporate Health Centre’s key healthcare institution, which is expected to service 20,000 people in the Norilsk Industrial District in twelve basic areas of medicine, including general practice, ultrasonography, cardiology, neurology, endocrinology, and more. The facility is slated to open in 2021. The repair is underway, while state-of-the-art medical equipment is being prepared for delivery. Investments in the project stand at ca. RUB 200 mln.
In 2021, Polar Division's medical facilities are also going to be repaired and provided with modern medical devices. All the facilities will be brought in compliance with corporate standards. Investments in the programme stand at ca. RUB 300 mln. Starting from 2022, similar activities will be rolled out at Nornickel’s medical facilities in the Norilsk Industrial District and Kola MMC.
As part of its corporate healthcare development programme, the Company plans to build another three medical centres in Norilsk (namely in Kayerkan, Talnakh, and the Central District) with a total area of 6,000 m2. The Group came to an agreement with Monchegorsk municipal authorities to erect a new modern polyclinic building and open Nornickel’s corporate healthcare facility, which will admit both employees of the Company and locals.
Developing a medical information system
The Corporate Healthcare project stipulates the implementation of a dedicated information system to be installed across all medical facilities of the Company, including health resorts in different regions. This will help to set uniform medical care standards and prevent undesired consequences of the lack of information for treatment.
Key functions of the dedicated medical information system:
- create a shared information environment enabling medical professionals to have joint access to employees’ electronic health records (EHR);
- improve the efficiency of corporate healthcare facilities through business process automation using a shared platform and integration with federal and regional healthcare services;
- create a predictive data analysis tool to identify risks of disease occurrence or development at any phase of healthcare.
The system will function in accordance with applicable Russian laws, including Federal Law No. 152-FZ On Personal Data dated 27 July 2006 and Federal Law No. 187-FZ On the Security of Critical Information Infrastructure dated 26 July 2017. Smooth operation of the system is underpinned by state-of-the-art and reliable equipment securing protection against any potential leakage of employees’ personal and health data.
OHS control and prevention
To improve safety culture and prevent workplace injuries, Nornickel regularly takes control and prevention measures, including: 403-2 403-3
- second-party OHS management audits (crosscompany audits of the Group companies involving the OHS heads and experts from other Group companies);
- internal OHS management audits;
- OHS monitoring at each facility, including multiphase production site control and ad hoc, targeted and comprehensive OHS inspections;
- safety behaviour audits;
- compliance and certification audits as part of the OHSAS 18001:2007 and ISO 45001:2018 management system;
- independent external audits of the OHS management system and occupational safety culture.
Health and safety performance indicators for accident prevention
Indicators | 2016 | 2017 | 2018 | 2019 | 2020 |
---|---|---|---|---|---|
Audits conducted: | |||||
by health and safety committees (thousand) | > 31.5 | > 30.8 | > 30.9 | > 29.8 | > 48.5 |
Target audits conducted by managers, senior specialists and committees of the Group's facilities and business units (thousand) | 6.8 | 8.7 | 9.7 | 9.6 | 10.6 |
Ad hoc audits (thousand) | 8.8 | 15.3 | 15.7 | 15.5 | 27 |
Comprehensive audits of health and safety and relevant management systems | 167 | 221 | 149 | 126 | 164 |
Coupons removed from the books of employees violating health and safety requirements (thousand)* | 3.4 | 2.9 | 2.2 | 1.8 | 1.1 |
Employees subject to disciplinary action for the violation of health and safety requirements (thousand) | 8.8 | 7.9 | 6.8 | 6.3 | 5 |
Employees with reduced bonus payments (thousand) | > 15 | > 13.6 | > 13 | > 11.9 | > 10 |
Total (RUB mln) | > 55 | > 74 | > 70 | > 69 | > 59 |
Employees incentivised for health and safety involvement and lower workplace injury rate as per the audit results (thousand) | > 5 | > 5.6 | > 6.4 | > 6.5 | > 5 |
Total (RUB mln) | > 51 | > 41 | > 52 | > 57 | > 59 |
Health and safety competitions
In 2020, we launched team and individual competitions in occupational health and safety in line with the internal HSE standard. Team competitions were held across seven groups of Nornickel’s production facilities.
Results of individual competitions were announced with the following awards granted:
- Best Health and Safety Head;
- Best Health and Safety Line Manage;
- Best Health and Safety Specialist;
- Best Health and Safety Compliant Worker.
The Company also runs an ongoing Safe Work communications programme. In 2020, it focused on:
- media support of key OHS initiatives;
- demonstration of the management’s commitment to occupational safety (media publications, management meetings with employees);
- updating OHS information on the corporate portal;
- covering OHS competitions and announcing the best OHS manager, expert, and workplace;
- making employees aware of the existing OHS situation in the Company, accidents, investigations, and actions taken.
Engagement of employees in safety management
Most of the Group companies have in place joint health and safety committees (councils) made up of the management, employee and trade union representatives. The Group companies operating such joint committees employ over 70,300 people (around 97.2% of the Group’s total headcount). The Head Office does not have a joint committee (as there is no trade union in place, but representatives of the Norilsk trade union take part in the HSE Committee meetings). On top of that, Norilsk Nickel Corporate University (an educational institution not involved in production) and NordStar Airlines (no proposals from trade unions have been received, setting up a joint committee in 2021 is currently under consideration) do not have committees.
Authorised representatives of trade unions and staff in occupational health and safety (996 employees) were elected to participate in preventive activities across the Group’s production units. In 2020, they took part in over 20,000 audits and submitted more than 6,000 health and safety improvement proposals.
Health and safety topics covered in formal agreements with trade unions
The Group and most of its production companies entered into collective bargaining agreements with employee representatives (including trade union organisations). The collective bargaining agreements contain relevant occupational health and safety provisions and cover some 69,900 Group's employees (approximately 96.6% of the Group's total headcount).
OHS training
One of the key strategies to increasing occupational safety is improving OHS qualifications of staff. To this end, Nornickel organises regular briefings on and training courses in occupational health for its employees.
In 2020, OHS pre-certification briefing, basic training and certification covered 34,000 employees of the Group. The Group’s health and safety training expenses exceeded RUB 76 mln.
We introduced dedicated software modules for mining jobs (LHD operator, hole driller, production face mining worker, electric locomotive driver, blaster, tipple operator, conveyor operator, slinger, electric and gas welder, dock operator, furnace operator) in order to provide health and safety briefings
Polar Division, Polar Construction Company, Kola MMC, Norilsk-Taimyr Energy Company, Norilsknickelremont, Medvezhy Ruchey, Norilsk Production Support Complex, and Pechengastroy use comprehensive Pre-Shift Examiner systems designed to test and consolidate the knowledge of applicable safety requirements for different disciplines. Employees are required to pass a test before starting their work shift.
In 2020, as part of the project to develop and implement a professional competency model for managers and specialists of OHS functions, we conducted pilot testing (knowledge and skills tests) of managers and specialists of HSE Departments at the Head Office, Polar Division, and Kola MMC. Results are used to assess the adequacy of the competency model. Testing is also planned for other Group companies.
All new hires take an induction training course under a dedicated OHS programme regardless of the length of service in their profession..
Workplace injuries
The Group’s Health and Safety Strategy, which was reviewed and approved by the Audit Committee of the Board of Directors in 2014, lays out plans to reduce production-related accidents in absolute terms every year, pursuant to Russian labour laws.
Bringing fatal production-related accidents down to zero is one of the strategic objectives to be reached in the course of implementing the Health and Safety Strategy.
All workplace accidents are investigated in accordance with applicable Russian laws. Investigation results serve as a basis for developing measures to be taken promptly to eliminate the root causes. 403-2
In order to define priority paths for further improvement of the corporate health and safety management system and mitigate injury and accident risks across Nornickel’s key assets, an independent company has been assessing the level of the Company’s industrial safety culture every year since 2014. In the recent seven years, our safety culture level (a Bradley Curve indicator) has improved from 1.4 to 3. Improvements in the safety culture metrics were driven by greater personnel involvement in occupational health and safety, OHS leadership exemplified by the management, and stronger risk assessment and management expertise.
Emergency preparedness
The Group operates over 300 hazardous production facilities and uses various hazardous substances in its processes. These facilities comply with Federal Law No. 116-FZ On Industrial Safety of Hazardous Production Facilities dated 21 July 1997 (“Federal Law No. 116-FZ”), and ensure preparedness for emergencies, including emergency containment and response.
The underlying document for emergency containment and response plans is the Regulation on Containment and Elimination of Accident Consequences at Hazardous Production Facilities approved by Resolution No. 730 of the Russian Government dated 26 August 2013. They are approved by heads (deputy heads) of production units that operate such facilities, and heads of regional emergency rescue services and units.
The plans are reviewed and approved in a timely manner, their effective periods being:
for underground mining facilities | 6 months |
for open-pit mining and concentration facilities | 1 year |
for hazard class 1 facilities* | 2 years |
for hazard class 2 facilities | 3 years |
for hazard class 3 facilities | 5 years |
Key workplace injury indicators
Indicator | UoM | 2016 | 2017 | 2018 | 2019 | 2020 | Change in 2020 y-o-y, % |
---|---|---|---|---|---|---|---|
FIFR | 0.11 | 0.08 | 0.05 | 0.08 | 0.08 | — | |
LTIFR | 0.35 | 0.44 | 0.23 | 0.32 | 0.21 | -34.4 | |
Total workplace injuries as per Russian labour laws | No. | 56 | 61 | 32 | 44 | 30 | -31.8 |
Fatal workplace injuries | No. | 13 | 9 | 6 | 9 | 8 | -11,1 |
Minor injuries | No. | 719 | 719 | 1,043 | 1,000 | 788 | -21.2 |
Potentially dangerous incidents | No. | 1,845 | 1,711 | 2,270 | 2,220 | 1,751 | -21.1 |
Occupational diseases | No. | 339 | 361 | 318 | 290 | 235 | -19.0 |
In order to ensure readiness for containment and response at hazardous production facilities, Polar Division signed contracts with a professional mine rescue unit for mine rescue services and the maintenance of auxiliary rescue teams’ equipment. Auxiliary mine rescue teams were set up at Polar Division’s and Kola MMC’s hazardous production facilities (hazard classes 1 and 2) engaged in underground mining operations, as required by Federal Law No. 116-FZ and the Procedure for Establishing Auxiliary Mine Rescue Teams approved by the EMERCOM’s order No. 765 dated 29 November 2013.
At the Group's hazardous production facilities, training sessions are held regularly and personnel are trained to deal with accidents, incidents, and emergencies.
Group companies have provisions for emergency containment and response at hazardous production facilities (MMC Norilsk Nickel allocated RUB 100 mln, Polar Division — RUB 50 mln, Kola MMC — RUB 50 mln, Norilskgazprom — RUB 18.578 mln, Lesosibirsk Port — RUB 10 mln, Norilsk Production Support Complex — RUB 5 mln, Medvezhy Ruchey — RUB 5 mln, Yenisey River Shipping Company — RUB 4.4 mln, GRK Bystrinskoe — RUB 3 mln, TFC — RUB 3 mln, Krasnoyarsk River Port — RUB 1 mln, Norilsk Airport — RUB 500,000, Vostokgeologiya — RUB 200,000, Gipronickel Institute — RUB 200,000, and Murmansk Transport Division — RUB 117,000).
Polar Division, Medvezhy Ruchey, Norilsk Production Support Complex, GRK Bystrinskoe, and Kola MMC hazardous facilities put in place surveillance, warning, communication, and support systems to be fully prepared for emergency containment and response. Mines are equipped with radio and positioning systems for employees, and telemetry system for underground machinery to track their locations. Hazard class 1 and 2 facilities operate local warning systems.
In 2020, following the incident at HPP-3, Group companies revised their emergency containment and response plans at hazardous production facilities, as well as oil and petroleum products spill response plans in 2020—2021.
Emergency preparedness system at hazardous production facilities
EMERGENCY CONTAINMENT AND RESPONSE PLANS AT HAZARDOUS PRODUCTION FACILITIES (HAZARD CLASSES 1, 2, 3) | |||
Agreements with professional emergency rescue services and organisations across the Company’s footprint | Auxiliary mine rescue teams at Polar Division and Kola MMC. Monthly training and exercises in near-real conditions | Drills involving employee and emergency rescue services | Provisioning for emergency containment and response at hazardous production facilities |
NORNICKEL GROUP COMPANIES HAVE SURVEILLANCE AND WARNING SYSTEMS, AND SYSTEMS FOR COMMUNICATION AND SUPPORT IN CASE OF AN ACCIDENT |
Improving the emergency response system in 2020—2021
Norilsk Nickel Group’s companies | Activities |
---|---|
Polar Division of MMC Norilsk Nickel | Key activities in 2020:
|
NTEC | Plans for 2021:
|
Medvezhy Ruchey LLC | Key activities in 2020:
|
Norilskgazprom | Key activities in 2020:
|
Norilsktransgaz | Key activities in 2020:
|
Krasnoyarsk River Port» | Plans for 2021:
|
Norilsk Airport |
In 2020, maintenance repair of 1000 m3 vertical steel tanks was carried out for RUB 2.1 mln. Plans for 2021:
|
Social policy
The Nornickel Group offers its employees – many of whom work beyond the Arctic Circle – a wide range of benefits and social care support. They are provided on an ongoing and consistent basis, taking into account employee feedback. 403-6
The social package includes the following benefits and compensations:
Social expenses and benefits, RUB mln
Plan
Actual
Plan
Health improvement programmes
The harsh climate of the Far North and the nature of operations at the Group’s facilities require special care for the health of employees, putting health improvement and wellness programmes among the priorities of Nornickel’s corporate social policy. For many years, the Company has been implementing programmes of rehabilitation and health resort treatment for its employees and their families. 403-6
The unfavourable epidemiological situation had an impact on a summer recreation programme traditionally run for children of the Company’s employees to spend some of their holidays at the Vita Health Resort in Anapa. The Company organised local summer activities by launching virtual camps for kids in the Murmansk Region, Norilsk and Dudinka.
In the Murmansk Region, children aged six to 16 were able to join the FUTURE CAMP. Some 100 children took part in online educational and entertainment events over two 2-week sessions. Due to restrictions on mass events and gatherings that were in place during the autumn break at local schools, we held another online session, this time 1-week-long, attended by 75 kids.
Moreover, Nornickel supported a virtual camp organised by the early career guidance foundation Zelenaya Kistochka (Green Brush) for children from seven to 15 years old in Norilsk and Dudinka. Around 80 kids took part in the programme. The foundation’s lecturers, psychologists and subject-matter experts held more than 80 webinars on environmental protection, geology, and health and safety. After the summer session, the children were invited to develop eco-projects and present them in November. Over 40 projects were highly praised by the jury. The winning drawings and paintings were used in a series of printed materials and souvenirs by Zelenaya Kistochka. All winners received diplomas and prizes.
Co-Funded Pension Plan Programme
Nornickel’s employees are offered an opportunity to join the Co-Funded Pension Plan, a corporate private pension programme. As at the end of 2020, it covered 11,519 employees across 21 Group companies, with 5,325 retirees already receiving pensions. 201-3
The programme provides for two pension plans: Parity and Corporate. Under the Parity Plan, pension savings are co-funded by the employee and the Company on a par (equal) basis. The Corporate Plan is designed for highly skilled employees and/or employees with highly sought-after occupations; within this plan, Nornickel finances private pension plans for such employees.
In 2020, an average participant contribution amounted to 3.23 % of the employee’s salary, or the Company’s monthly average of RUB 4,037.
Participants of the Co-Funded Pension Plan, by region
Plan
Actual
Plan
Co-Funded Pension Plan highlights
Housing programmes
In 2020, the Company continued the combined Our Home / My Home programme, with its participants* able to acquire ready-for-living apartments on special terms across Russia. Since the start of the programme, 3,826 apartments have been provided to the Company’s employees.
To do so, Nornickel purchases ready-for-living apartments in various Russian regions at its own expense and provides them to eligible employees under co-financing agreements. The Company pays up to a half of the apartment cost (but in any case no more than RUB 3 mln), with the rest paid by the employee within a certain period of employment with Nornickel Group (from five to ten years). The cost of housing remains unchanged for the entire period of the employee’s participation in the programme. Property titles are registered at the end of the employee’s participation in the programme, but the employee may move in immediately after receiving the apartment.
In 2020, Nornickel also carried on with the Your Home initiative based on similar arrangement as the Our Home / My Home programme, i.e. payment by instalments and up to a half of the apartment cost covered by the Company. The only difference is that the title to Your Home properties is registered right after the purchase but is burdened with a lien to be held by the seller until the employee fully pays up the entire cost of the apartment and their participation in the programme ends. The apartments are purchased by the Company in the Moscow and Tver regions and the city of Yaroslavl and allocated to employees after their commissioning upon completion of construction. Since the start of the programme, the Company has purchased 1,789 apartments.
Support to new employees
Nornickel provides support to newly employed staff relocating to Norilsk and the Taimyrsky DolganoNenetsky Municipal District, including young specialists, workers, engineering staff and managers.
It also offers them financial assistance and reimburses relocation expenses, baggage fees, and living costs for the first three years. On top of that, the Company also pays a one-time relocation allowance to support employees at the new place of work. With 364 employees joining the relocation support programme in 2020, it now has a total of 829 participants.
In 2020, Nornickel launched Onboarding, an automated system to assist new employees and managers during their first months at the Company. It is now being piloted at several Group companies and the Head Office and has 1,348 users. A rollout across the rest of the Group is scheduled for 2021.
Sporting and mass public events programme
Nornickel promotes sports and a healthy lifestyle to recharge the corporate team spirit and maintain a positive work environment. It organises sporting events and competitions attended by its employees, their families, and the local community. 403-6
We have teamed up with various federations to support sports in our regions of operation. Our partners provide training support to coaches, give master classes, and promote healthy lifestyles.
Since 2018, Norilsk Division has been hosting the Night Time Hockey League, with the Company’s employees taking part in the games. Every year, ten teams compete for the opportunity to take part in the Russian National Ice Hockey Festival for amateur teams.
The events run by the Company also include the annual Polar Division Olympics, Kola MMC Olympics, Norilsk Nickel Ski Track health marathon, “Dad, Mum and I – a Sporty Family” corporate competition, swimming, ice hockey, futsal, volleyball, basketball, alpine skiing, snowboarding competitions, and sport events dedicated to the Metallurgist Day and other high days and holidays. Nornickel’s employees can choose from an increasingly wide range of sports.
In 2020, the Company’s management decided to cancel the majority of sports events due to the pandemic.
Our sports and fitness events drew a total of 11,100 employees in 2020 – 6,700 took part in spartakiads and mass sports events in Q1 2020 and 4,300 attended sports and fitness events online.
In April 2020, we launched the year’s first online project – Immune Charge. It featured online contests and flash mobs, such as NN_workout, Nornickel’s Sporty Family and My Family.
NN_workout, for example, is a marathon that promotes healthy lifestyles and encourages staff to exercise at home to keep fit and boost immunity. Our employees have also been more and more enthusiastic about health marathons and sports events organised by municipal authorities.
Programmes supporting former employees and their families
The ongoing support of its former employees is part of the Company’s corporate social policy
The Company’s Veterans programme has been designed to support unemployed pensioners who permanently reside in Norilsk. The terms of participation depend on the employee’s length of service or permanent disability status. Financial aid is paid from the charitable contributions made by the Company.
The former employee financial aid programme establishes the amount of the benefit paid upon retirement by reference to the employment period
The Pensioner Financial Aid Fund grants financial aid to former employees who retired prior to 10 July 2001 provided they had been employed by the Company’s units for more than 25 years and permanently reside outside of the Norilsk Industrial District. The Fund relies on voluntary monthly contributions from employee salaries and equal charitable contributions from the Company’s budget.
The Company also provides targeted assistance to its former employees and their families to pay for health improvement and medications, funeral services, and helping in financial distress.
Improvement of social and working conditions
At Nornickel, we place a strong emphasis on improving the living and working conditions of our people and strive to create a comfortable working environment. The Group companies operate more than 3,200 sanitary, amenity, sports and fitness, catering, healthcare, and recreational facilities with a total area of over 350,000 m2.
From 2003, the Group has been implementing the programme to improve social and working conditions. Since its launch, we have overhauled 417 social facilities and purchased 432 relocatable buildings, investing a total of RUB 6,562.1 mln.*
In 2020, we finished renovating and delivered 138 social facilities and purchased eleven relocatable buildings. The Company improved working conditions for 3,651 people. The programme’s costs amounted to RUB 1,023 mln. We have issued a standards handbook featuring a single exterior and interior design concept that will be implemented throughout our production facilities from entrance checkpoints to the individual workplaces.
In 2021, Nornickel plans to spend RUB 2,182 mln to overhaul 157 social facilities and purchase 13 relocatable buildings. The Company also expects to roll out and implement new corporate design solutions for social facilities, hire major contractors for three years’ work in the Norilsk Industrial District and take measures to optimise and speed up the programme.
As part of the programme for 2021–2023, we plan to overhaul and equip over 300 different social facilities, including administrative and sports facilities and canteens, with over RUB 5.5 bn in investment.
Social facilities overhauled in 2003–2020
Social support to employees facing redundancies due to closure of production facilities
In late 2019, the Group decided to shut down its smelting facilities in the town of Nickel on the Kola Peninsula with a view to ensuring compliance with the environmental regulations and improving environmental conditions in the Pechengsky District of the Murmansk Region.
The smelting production closure will affect 660 employees of Kola MMC (Smelting Shop and support services) and Pechengastroy.
In December 2019, Nornickel developed a programme of social support for the smelting operations personnel facing redundancies, making the commitment to support them in relocating to a new place of residence, retraining, and further employment. This commitment was agreed with the Social and Labour Council and trade union organisations of Kola MMC and Pechengastroy.
In 2020, the Company launched its dedicated Nornickel Employment Centre, which is focused on providing comprehensive support to the workers facing redundancy due to the smelting operations closure (including information, consulting, and career guidance support) and cooperating with the divisions of Nornickel Group, regional authorities and employers in the Murmansk Region on employment opportunities for its redundant workers.
All staff-related measures were taken in compliance with the requirements of labour and employment legislation and our social support programme. In 2020, the Company’s total spending under this programme amounted to RUB 478.3 mln, with RUB 402.1 mln paid to 241 redundant employees as compensation for unused PTO days or in the form of severance pay or financial aid. Moreover, 265 employees were re-employed within the Group at the same salary for up to one year and with reimbursement of relocation costs. They also received financial aid for their housing purchases and were trained, retrained or evaluated for their new professions or jobs.
In late 2020, the Company’s management decided to shut down Severonickel Plant’s copper refining facility (part of Kola MMC) in 2021. A total of 701 employees of Kola MMC and Pechengastroy are affected by this decision. We plan to extend our current support programme for smelter workers to those facing redundancy due to the copper refining facility closure.
Key social support programme benefits 404-2